
SUBSCRIBE TO THE NEWSLETTER
Receive updates about our latest products, application reports and white papers - right in your e-mail inbox!
Starting Situation
Minor design changes to the sheet metal always occur during production start-up. This can be, for example, the optimization of a connection point for easier assembly of the sheet metal. If the resulting tool changes are implemented manually, it is often not possible to achieve the desired geometries with sufficient accuracy. In the present application, a circular embossing is too close to the edge of the sheet metal, which leads to an irregular trim edge. This problem is solved by extending the embossing to the edge of the sheet.
The time pressure was high, as the customer wanted modified sheets for the next delivery. However, the tool was only available one week before the pressing date. In addition, we only had access to CAD data for the sheet metal, but not for the tool itself, which meant that no milling planning could be carried out in advance. A conventional process would not have been possible without transporting the tool to a large milling machine and the schedule could not have been met. In addition, the milling volume was small. On a conventional machine, the set-up times would have been higher than the milling time, which would have been an inefficient use case of the expensive machine.
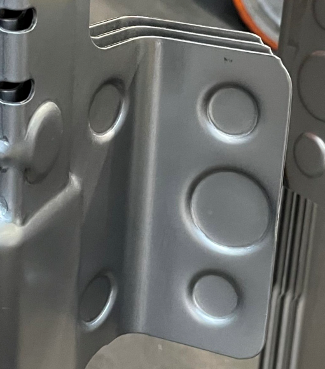
Procedure
Our team worked hand in hand to keep to the schedule. Immediately after the tool was made available on Monday in the morning shift, a colleague digitized the tool with our Leica Absolute Tracker AT960 and Absolute Scanner AS1 and immediately afterwards built up material on one half of the tool. Due to the small size of the embossing, manual build-up welding was faster than using our picum-Lisa mobile welding robot. Using the scan data and CAD data provided by the customer for the sheet metal modification, another colleague designed adapted CAD surfaces and carried out the milling planning during the late shift. This meant that our mobile picum-Bart milling machine was able to start milling on time on Tuesday morning. The milling time per embossing, including set-up times, was only a few hours. Therefore, despite four different milling positions, we were able to hand over the tool for to our toolmakers for manual finishing and try-out.
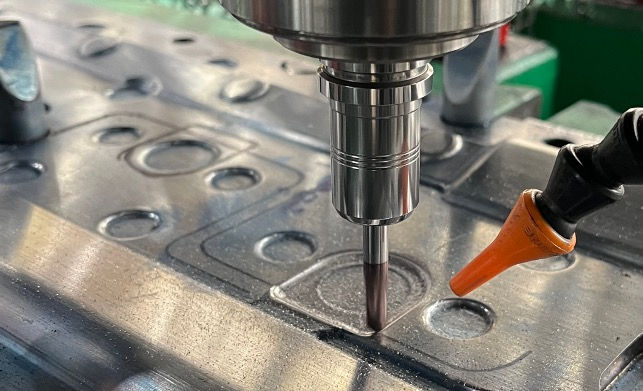
Advantages
We deliver the complete modification from a single source; from the adaptation of the CAD data to the final testing of the tools in the try-out press. Thanks to our flexible and well-coordinated team of different experts, we can also accept orders at short notice and process them without losing time due to coordinating different suppliers. Thanks to our mobile high-tech systems, everything takes place on your premises and you do not have to worry about transportation.
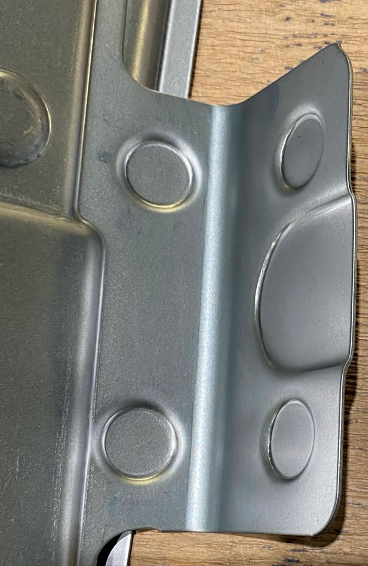