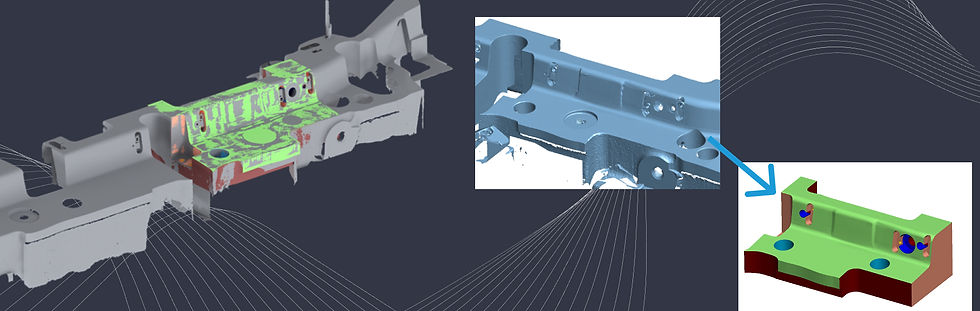
SUBSCRIBE TO THE NEWSLETTER
Receive updates about our latest products, application reports and white papers - right in your e-mail inbox!
Starting situation
Two heavily loaded blades of a cutting die in a tool had already been repaired several times due to wear and should be replaced to ensure the continued smooth operation of the tool. However, the entire trimming tool was a single casting that would be complex and expensive to replace. As it would also be necessary to rework the entire tool, production would have to be paused during this try-out phase, resulting in additional costs. The design and manufacture of a new insert for the cutting die, which is integrated into the existing tool and replaces the two problematic cutting blades, is a cost-effective alternative. Due to our broad know-how, Picum was ideal for the realization of this project.
Procedure
At the start of the project, we recorded the actual condition of the tool in detail using measurement technology. We digitized the geometry of the entire tool with a 3D surface scan. There were also cutting bushes in the area to be replaced. Here we took tactile measurements with the Leica T-Probe. This mobile system is ideal for bores, pockets and other standard geometries that are difficult to capture with a laser scanner. We used the measurement data in the reverse engineering process to create new functional surfaces in CAD that reproduce the actual tool state as accurately as possible. Areas that are not directly functional surfaces, such as visible manually welded negative radii, were of course replaced with more aesthetically pleasing and easier to manufacture surfaces. We used the derived surface data to design the new insert for the cutting die, including the screw connection and connection surfaces to the old casting. It is important that the cutting bushes are positioned exactly, as the slider and cutting punch on the opposite side are not adapted.

Advantages
The new insert is much smaller and less complex than the entire casting. Therefore, the new production is also considerably cheaper. With the CAD data now available, the production of the insert for the cutting die could easily be outsourced. The tool was able to continue production in the meantime and only had to go to the workshop briefly to mill the seat for the new insert and drill the connection holes. As the insert was manufactured according to the measurement data, only minimal manual finishing was required, and the tool was able to resume production quickly. If the heavily loaded cutting die blades need to be replaced again, the effort would be much less the next time, as the insert can simply be manufactured and replaced using the CAD data now available.
We offer the complete modification from a single source:
Measurement of the current state of the tool
Design of the new insert and design of the modifications of the casting
Contracting of the production
Manual finishing and try out the tool with the new insert.