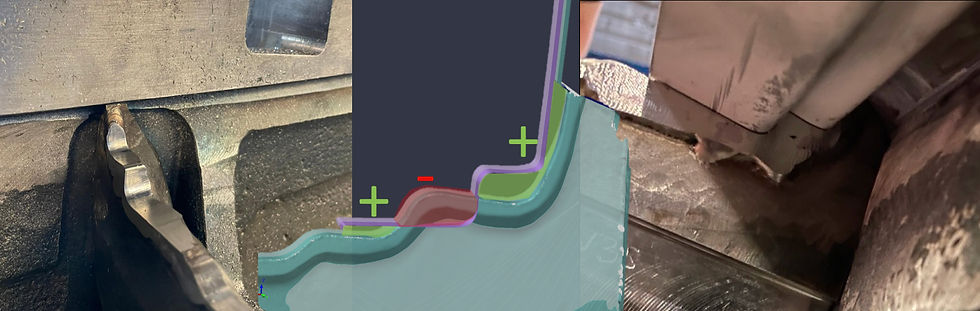
SUBSCRIBE TO THE NEWSLETTER
Receive updates about our latest products, application reports and white papers - right in your e-mail inbox!
Ausgangslage
Blechteile für die Fahrzeugindustrie unterliegen, gerade bei einer neu anlaufenden Serie, diversen Optimierungsprozessen in Bezug auf nachfolgende Produktions- bzw. Montageschritte. Weiterhin können Änderungen durch Designanpassungen oder zur Materialeinsparung im Fertigungsprozess sinnvoll sein. Um die gewünschte Änderung an einem Serienblechteil umzusetzen, müssen entsprechend die für die Fertigung eingesetzten, mehrere Tonnen schwere Werkzeuge angepasst werden.
Herausforderungen & Vorgehen
Im vorliegenden Anwendungsfall erforderte die Optimierung der Beschnittkontur eines Strukturblechs das Anpassen des Werkzeuges an mehreren Teilbereichen in der OP 30. Durch die neue Kontur kam es zu einer Kollision des Blechs mit dem Niederhalter. Außerdem waren zwei gehärtete Trennmesser auf die neue Form anzupassen, die nach einem Beschnitt den anfallenden Blechabfall teilen, um diesen problemlos aus dem Werkzeug abführen zu können. Um die Kollision des neuen Blechs mit dem Niederhalter zu verhindern, musste dieser über die gesamte Blechlänge von ca. 1000 mm, 30 mm breit und 35 mm tief freigefräst werden. Bedingt durch die Länge des Bereichs, wurde die Bearbeitung für unsere Maschine virtuell in mehrere Teilbereiche aufgeteilt, was durch die Nutzung eines Lasermessgeräts für das Referenzieren kein Problem ist. Die stückweise Bearbeitung wurde anschließend mit einem Picum System realisiert. Durch das Entfallen von Hin- und Rücktransport des Niederhalters zu einer großen Bearbeitungsmaschine wurde ein signifikanter Zeitvorteil erzielt. Das Bild unten zeigt einen Teil des freigefrästen Bereichs.
Das Angleichen der beiden Trennmesser auf die neue Blechform, jeweils ein Bereich von etwa 10 mm x 100 mm, war planerisch und in der Durchführung besonders spannend. Weil aus mehreren Gründen die für das neue Blech erstellten Konstruktionsdaten, wie häufig der Fall, für die Planung nicht genutzt werden konnten, wurde von Picum eine Änderungskonstruktion auf der Grundlage von eigenen Datensätzen vorgenommen. Da die vorherigen Operationsstufen des Werkzeugs schon auf die neue Blechgeometrie angepasst worden waren und somit viel manueller Nacharbeit Bleche gefertigt werden konnten, nutzten wir ein solches Teil für das weitere Vorgehen. Durch das Scannen der Oberfläche, des in die OP30 eingelegten Teils, mit Hilfe unseres Laserscanners, waren wir in der Lage, die grundlegenden Daten für die Änderungskonstruktion und die anschließende Bearbeitung zu planen. Die geänderte Beschnittkontur des Blechs machte es erforderlich, dass die Trennmesser in Teilbereichen sowohl ab- als auch aufgebaut, also neben dem Fräsen auch Material aufgeschweißt werden musste. Siehe Bild rechts. Für den Materialaufbau nutzten wir hierbei eines unserer mobilen robotergestützten Schweißsysteme, um direkt auf dem Grundwerkstoff mit einem Hartauftrag Material an den entsprechenden Stellen aufzubauen. So lässt sich ein gleichmäßiger Nahtaufbau und eine hohe Verschleißbeständigkeit der stark beanspruchten Messer sicherstellen. Anschließend wurden die abzubauenden Bereiche und das aufgeschweißte Material mit unserem mobilen Frässystem auf die erforderliche Soll-Geometrie abgefräst. Nach einer abschließenden Qualitätskotrolle der Bearbeitungsstellen konnte das Werkzeug direkt vor Ort dem Kunden übergeben und für die Produktion freigegeben werden. Das Bild zeigt den 3-D-Scan des Werkzeugs vor der Bearbeitung. Violett ist das gescannte Blech in Soll-Lage dargestellt. Der rote Bereich wurde entfernt, die grünen Bereiche hart aufgebaut und abschließend auf Endkontur gefräst. Bilder des Ergebnisses mit und ohne Blech sind oben auf diesem Blatt zu sehen.
Vorteile
Die für die Trennmesser in diesen Fall angewendete Strategie, die Datengrundlage anhand einer gescannten Blechkontur zu generieren, führte zu einem sehr guten Ergebnis bei geringer Durchlaufzeit und ist bei nicht‑formgebenden Elementen ein sinnvolles Vorgehen. So lässt sich unabhängig von CAD‑Daten direkt vor Ort arbeiten und es kann flexibel auf Änderungen reagiert werden. Besonders vorteilhaft ist dies vor allem, wenn sich ein Blechteil in einem laufenden Optimierungsprozess befindet. Spannend an diesem Beispiel ist auch die Kombination des Aufbaus einer komplett neuen Geometrie mit additiver Fertigung und dem Nachbearbeiten mit dem Fräsen mit einem mobilen System direkt vor Ort!